Inflow and infiltration (I&I) is excess water that flows into sewer pipes from stormwater (inflow) and groundwater (infiltration). In this blog post, we’ll break down the causes and best practices for treatment of I&I even further. This illustration shows the six main types of I&I:
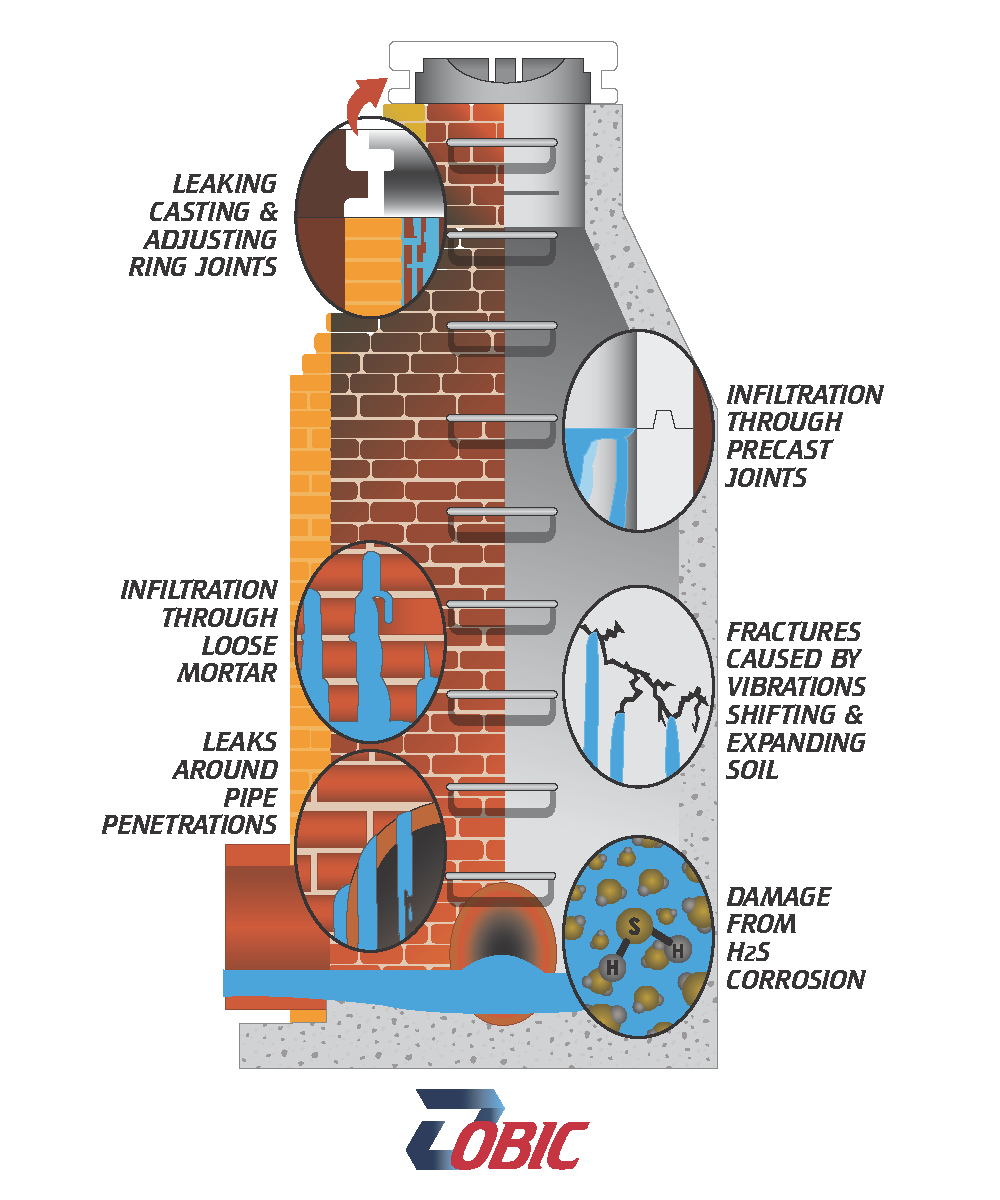
- Leaking Casting and Adjusting Ring Joints
Caused by: Manhole frames and covers or adjusting rings are installed to the cone section of the manhole with cement mortar. Because it is at the top near ground level, it’s exposed to freeze/thaw cycles, heavy vehicle loading, subsequent street paving, traffic vibration, and sometimes earth movement. All of these can cause the mortar to crack, creating voids with groundwater or rainwater infiltration. Other causes can include improper installation, cracked parts, and shifting mortar.
Warning signs: Infiltration is present, water marks on the wall, visible cracks, or sunken manhole lids (particularly annoying to taxpaying drivers). There may be staining or buildup from soil entering the manhole or calcium residue from leaking water. Additionally, freeze-thaw heaving can cause elevated covers, which can contribute to snow plow damage.
Options for repair/replacement: Historically, this issue was addressed by grouting the mortar joint or replacing the typical cast iron frames with polyurethane frames or adjusting rings, as they are more flexible. However, they are still affixed to the manhole cone with mortar, so they are still susceptible to future cracking. Another option would be to dig up and replace.
ART recommendations for treatment: We’re happy to provide rings and covers work as part of a comprehensive manhole lining job. The OBIC internal chimney seal is a monolithic (not a secondary component) polymer coating that’s sprayed all the way up and onto the underside of the manhole cover mounting ring. This completely seals the mounting joint and any stacked adjusting rings and provides a watertight fix to the infiltration problem. The flexible properties of the OBIC lining resist movement caused by freeze/thaw cycles, vibrations and soil movement, and it won’t come loose like other internal mechanical seals. Most importantly, the OBIC system does not require excavation, but external seals will require excavation.
- Infiltration Through Pre-cast Joints
Caused by: In order to comply with ASTM C478, pre-cast manhole sections are fitted with RAM-NEK® or similar gasket material to provide a watertight joint that inhibits infiltration through the joint. Over time, the gasket material degrades, stretches, washes out, or otherwise fails to prevent groundwater infiltration.
Warning signs: Infiltration/staining is present
Options for repair/replacement: Grout, cementitious application over the joint or internal lining, epoxy, rigid polyurethane, and bag liners can be used to treat the issue. While grout is less expensive up front, it has a shorter life span and only addresses the immediate area where it was injected. It cannot address any comprehensive corrosion control issues. Cement is widely used, and is less expensive than polymers, but it’s susceptible to cracking and often has adhesion failures. Epoxy is prone to cracking over time. Rigid polyurethane does not have any tolerance for moisture. Because it requires a completely dry substrate surface, it often fails to adequately adhere to the substrate. Bag liners are the most expensive option, as they require bypassing the sewer line, in addition to causing severe traffic disruptions.
ART recommendations for treatment: Lining has become the preferred way to treat if the structure is in good enough shape to do so. OBIC’s monolithic polyurea coating properly adheres to the substrate and stops infiltration through the joint.
- Infiltration Through Loose Mortar
Caused by: Mortar joints (cement) in brick manholes are susceptible to hydrogen sulfide gas present in the manhole environment, resulting in corrosion over time. In addition, other forces such as freeze/thaw cycles, traffic loading, and ground movement can all cause mortar joints to fail.
Warning signs: Infiltration is present and deteriorated areas are visible, such as missing mortar or bricks.
Options for repair/replacement: Tuck Pointing or Full Depth Lining with a cementitious material. Tuck Pointing is labor intensive and may result in the same deterioration over time. A cementitious application may also result in the same deterioration over time as you are replacing eroded cement with more cement.
ART recommendations for treatment: The OBIC multi-layer system is particularly beneficial for this problem as the middle layer of polyurethane foam expands to fill those brick mortar joints by sealing the crack or filling the missing mortar areas. This allows for a water tight seal that eliminates infiltration.
- Leaks Around Pipe Penetrations
Caused by: Typical pipe penetrations in a manhole are the sewer line at the bottom or a drain pipe that was installed with the manhole, or more likely, at a later date resulting in a substrate penetration. These penetrations are sealed with cement mortar that eventually cracks or deteriorates allowing groundwater to infiltrate. Other causes can include the shifting of ground or improper installation of the boot around the pipe, or the boot simply not being present.
Warning signs: Infiltration is present, water marks on the wall, visible cracks (older pipes have cracked concrete around this area), calcium buildup inside from leaking water, and sinking ground around the manhole
Options for repair/replacement: Cementitious patching around the pipe, chemical grouts, or Full Depth Lining. Patching around the pipe and chemical grouts only stop the water you can see during the application period. If the water table moves, infiltration may return. They also do not have the extended service life of a Full Depth Liner.
ART recommendations for treatment: In addition to the OBIC repair method, we will add an extension to the pipe penetration in order to provide a “pipe protrusion” that is away from the substrate wall and goes into the manhole. This allows a suitable amount of coating applied to the penetration area resulting in a water tight seal and protects against future movement or shrinkage. The OBIC Lining System provides the longest service life and most comprehensive protection of the structure.
- Fractures Caused by Vibrations, Shifting, and Expanding Soil
Caused by: Damage during installation/transportation of the components or ground movement. Texas, for example, is notorious for its dramatic soil movement due to its extreme wet/dry conditions. Clay soil acts like a sponge, expanding and contracting very quickly with changes in moisture, and it will be an additional force working to deteriorate manhole structures. In addition, even moderate earthquakes in any state can cause this. Vehicle traffic can also cause vibrations that can result in structure cracking over time.
Warning signs: Infiltration is present with visible fractures in the structure’s sidewalls
Options for repair/replacement: Removal and replacement of the damaged component or Full Depth Lining. Removal and replacement of the components are disruptive to the surrounding residential areas and traffic, but occasionally is warranted when a structural repair is necessary. Full Depth Lining with OBIC products will repair the infiltration and also provide protection in other areas such as joints and chimneys.
ART recommendations for treatment: OBIC lining systems fill cracks and missing mortar joints stopping the infiltration and restoring structural integrity.
- Damage From H2S Corrosion
Caused by: Hydrogen-sulfide corrosion occurs as an acid attack caused by the biogenic conversion of hydrogen-sulfide gas to sulfuric acid when moisture is present. Of course, there is always moisture present in a sewer system. Sulfuric acid is highly corrosive to the concrete surfaces commonly used to construct sewer collection systems. When that highly corrosive sulfuric acid runs down the wall of a concrete manhole over time, it will begin to erode the concrete surface and eventually erode several inches of thickness and lessen the structural integrity.
Warning signs: Deteriorated surfaces showing exposed aggregate and a mushy debris, white ash-like substrate on walls or benches, exposed structural rebar, and in the case of a brick structure, the cement mortar is eroded and/or missing.
Options for repair/replacement: Replacement may be necessary for structural ability. Grout or a cementitious application can also be used to treat the issue. Cement is an inferior fix because the original structure or mortar for a brick manhole is cement, so the same issue will occur again and again.
ART recommendations for treatment: OBIC polyurea liner systems are all resistant to hydrogen sulfide gas as polymers are not attacked by hydrogen sulfide. This makes them more suitable than cement-based liners and will prevent any corrosive damage caused by hydrogen sulfide. Replacement will resolve the structural issue, but the new structure will still need to be lined with an H2S resistant lining.
See first-hand how our manhole lining systems can stop infiltration and restore structural integrity. Sign up for a free product demonstration at www.artcoatingtech.com/contact-us or call us at 419-636-2684.